Three Steps to Reap the Full Benefits of Worker Safety Programs
To understand how to remove sources of friction and reap the benefits of improved worker safety, consider these valuable lessons.
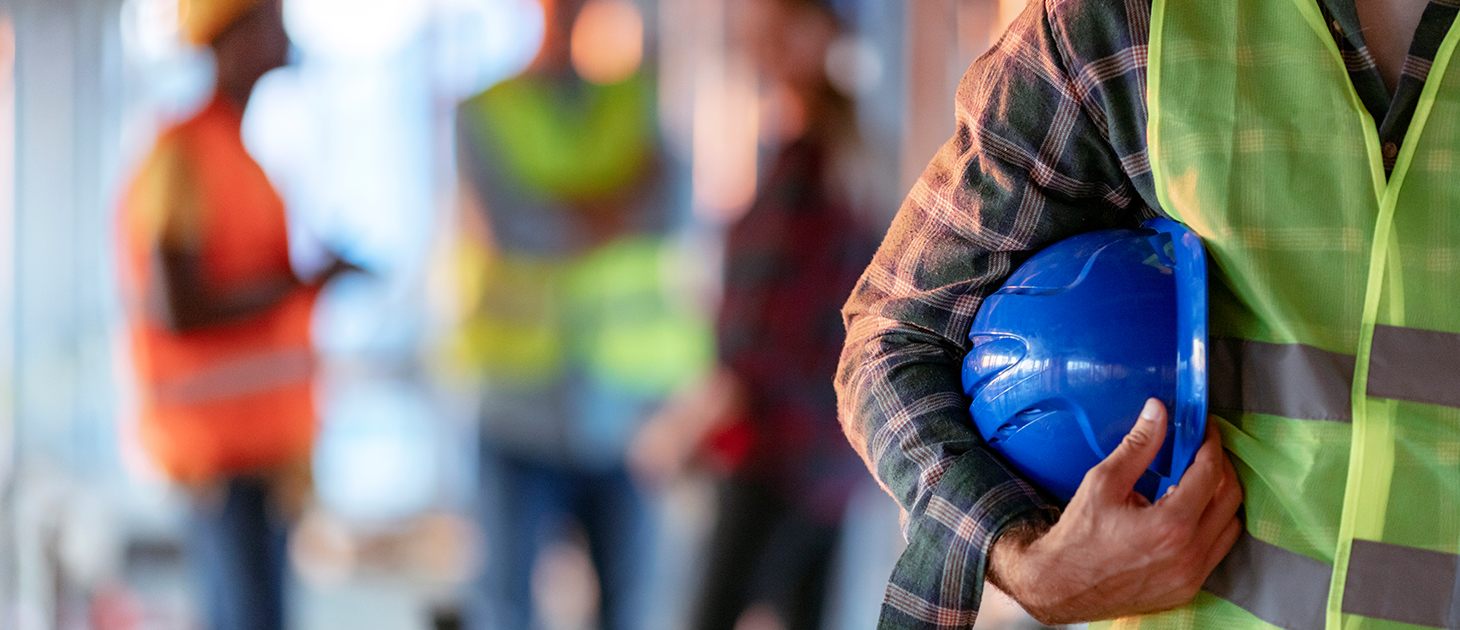
This article is sponsored by QBE North America.
Few would contest the importance of worker safety programs and the benefits of fewer injuries, higher employee morale and productivity, and lower workers’ compensation costs. But what sounds good in theory too often gets lost in practice. As companies grow and their organizations become more complex, so do the possibilities for organizational friction that reduces the effectiveness of worker safety programs.
Friction can develop at many levels. Senior management may delegate responsibility to mid-level leaders but provide limited support as improved safety measures are launched. There may be high turnover in the mid-level leaders charged with developing worker safety programs. The managers of workers “on the ground” may pay minimal attention to the directives from worker safety leaders, feeling they know what’s really happening in the workplace.
To understand how to remove these sources of friction and reap the benefits of improved worker safety, the experience of one manufacturer offers three valuable lessons that apply to many different industries.
Identify the Issue Precisely
The manufacturer brought in a new risk manager who noticed that two of their main factory sites had unusually high workers’ compensation losses. Historical efforts at the company had been focused on post injury management, such as getting the claims reported quickly and efficiently and helping workers return to work in limited or full capacity as soon as possible. But the efforts hadn’t made much difference.
To further analyze the issue, the risk manager met with the Claims and Loss Control experts from its insurance provider. The discussion led to the conclusion that the company had tried to implement safety measures at a macro level, such as accident investigation, ergonomics and other measures, but they were never taking root within the organization, partly due to high turnover of safety and HR people at the problematic plants.
From this discussion, the risk manager and Claims and Loss Control experts decided to dig deeper at a micro level to better understand the various issues at the different locations. As a result, the team devised and then carried out a strategy to map and track loss frequency and severity by plant location, specific location within the plant, type of injury, speed of reporting, and injured worker background and demographics. The team also physically inspected the plants to further identify risk factors and behaviors that could raise the risk of loss.
Quantify the Benefits for Management
Based on this analysis, the insurer’s team helped the risk manager develop a targeted service plan including Claims Management and Ergonomics. This helped to reduce large loss potential as well as reduce lost time claims and disability days. The key was to quantify the benefits and present them to the company’s president to get buy-in and active support in communicating the importance of execution through all levels of the organization.
Connect with the Culture at the Point of Risk
To avoid the company’s past failures, the team also realized the need to better understand the culture at the plants. The risk manager leveraged the reputation of the insurer’s team as outside, neutral party experts and had them interview the supervisors at the plant about the safety culture and how the managers dealt with employee injuries.
The team approached the supervisors in a non-judgmental way that made them more open to contributing to and implementing the targeted safety measures at the ground level. As the program in one plant took root and results improved, the team built trust and could leverage the success to help the risk manager expand the teamwork and risk modeling techniques throughout their organization.
By precisely identifying the issues, developing a solution with quantifiable benefits, and engaging the organization at all levels, the company reduced its incurred losses the next year by more than 90%. Moreover, those results proved sustainable in subsequent years. While such a dramatic improvement is unusual, there is no doubt that many companies could substantially benefit from taking similar measures both in terms of worker safety, workers’ compensation costs and higher productivity.
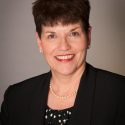
Theresa Everett is an assistant vice president, lead claims relationship manager at QBE North America, a global insurer.
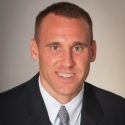
James Vachon is an assistant vice president, risk solutions manager at QBE North America.