General Motors Pivots to Mask-Making with Help from Dukane
Midsize companies are helping large corporations pivot their operations to manufacturing personal protective equipment needed for the fight against COVID-19—and, in some cases, producing it themselves.
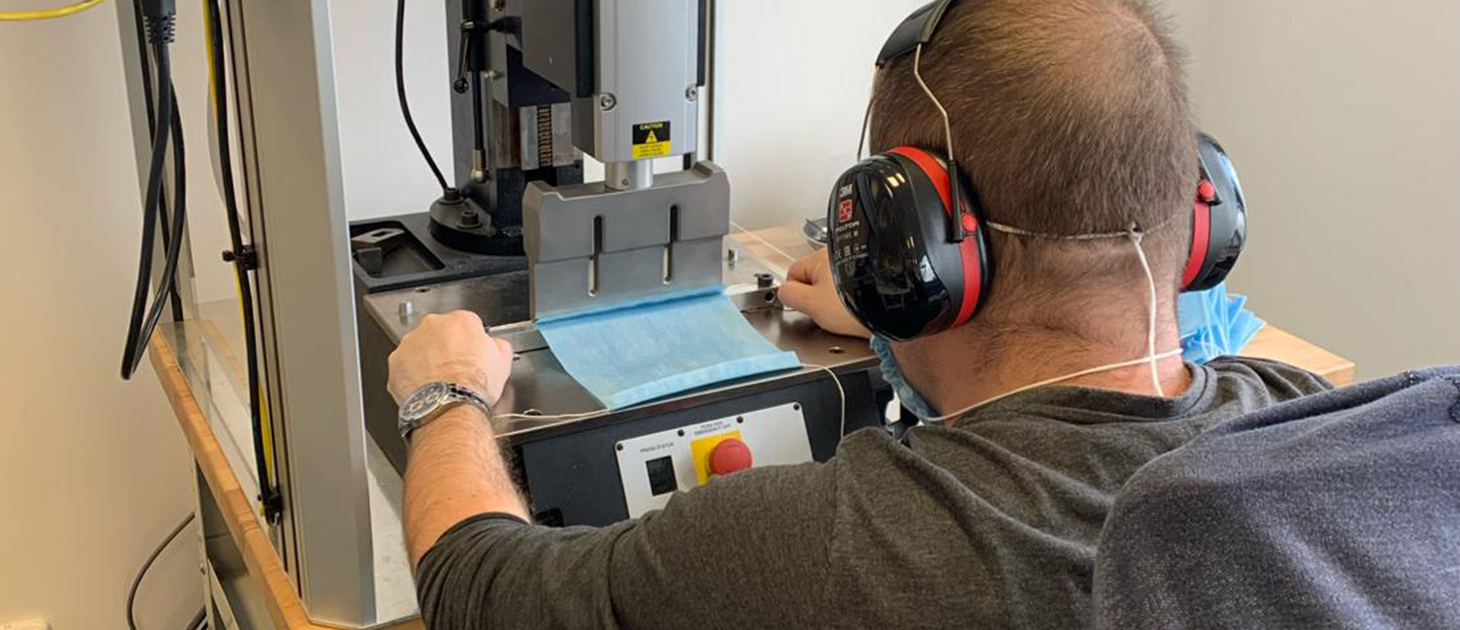
This article is part of an ongoing series about the ACG community’s contributions during the coronavirus pandemic. Have a story to tell? Reach us at editor@acg.org.
As businesses worldwide shift to manufacturing personal protective equipment needed for the fight against COVID-19, often it’s the household names that make headlines. But operating behind the scenes are midsize companies that are helping large corporations pivot their operations and, in some cases, they’re producing PPE themselves.
Last month, General Motors converted a decommissioned factory for producing transmissions into a facility for mask production in less than a week. To design and assemble the machinery needed, GM collaborated with Esys Automation, a JR Automation company.
On Sunday, March 22, JR Automation contacted Dukane, a manufacturer headquartered in St. Charles, Illinois, that makes equipment used for welding plastic, seeking the company’s ultrasonic bonding equipment for use in the GM factory. The catch: They needed the first systems in two days.
In order to qualify, design, model and test the units ahead of the aggressive deadline, Dukane shifted other projects and brought in additional workers. It shipped the equipment on Tuesday, March 24.
“Setting up a big manufacturing line like that, in that period of time, is unheard of, really. It’s extremely rare,” says Jim Gaittens, managing director of TVV Capital, Dukane’s private equity partner. Gaittens also serves as president of ACG Tennessee.
“Setting up a big manufacturing line like that, in that period of time, is unheard of, really. It’s extremely rare.”
Jim Gaittens
Managing Director, TVV Capital
Dukane shipped the remaining systems three days ahead of schedule. With that equipment in place, GM began production on April 6 and has since produced more than 620,000 masks, CNBC reported.
Making Masks
As a capital equipment manufacturer, Dukane sells its systems to customers like JR Automation. Until recently, the company didn’t produce end-products itself.
After the coronavirus outbreak began, however, Dukane’s country manager in the Czech Republic noted a shortage of masks following the Czech government’s mandate that citizens wear them in public starting March 18.
Through one of its channels, Dukane sells equipment for cutting and sealing nonwoven materials used for products like hospital gowns and disposable diapers. Amid the mask shortage, the company’s Czech plant set out to do something new: It would produce the masks itself, using donated materials.
“We knew we had the equipment and that we could utilize equipment to do it. The gap was, it’s not what we traditionally do,” says Jacob Kowalewski, Dukane’s global marketing manager.
Equipment orders kept the factory operating at full capacity during the workday, so employees—and in some cases, employees’ family members—worked after hours to produce the nonmedical-grade masks. (For safety, the group remained small and adhered to social distancing measures within the facility.)
Kowalewski estimates Dukane’s Czech facility has produced more than 100,000 masks. It consulted with the U.S. embassy in Prague, which helped connect the company with first responders, senior centers and other groups in need of donations. U.S. Secretary of State Mike Pompeo acknowledged Dukane’s contribution during his April 7 press briefing.
Stateside, a Dukane facility in Kimberly, Wisconsin, also has been operating after hours to produce face coverings to donate within the local community. Using technology employed for diaper manufacturing, the plant is making elastic scarves that wearers say are more comfortable than traditional face masks. The equipment can produce 3,600 scarves in an hour.
“That technology is great, and we know we have a market for it in the disposable diaper industry,” Kowalewski says. “What we’re seeing is that it’s really a good technology for [manufacturing] some other pieces.”
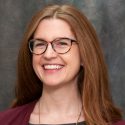
Kathryn Mulligan is the editor-in-chief of Middle Market Growth.