Anatomy of a Proterra Bus
Take a look inside Proterra's zero-emission electric buses.
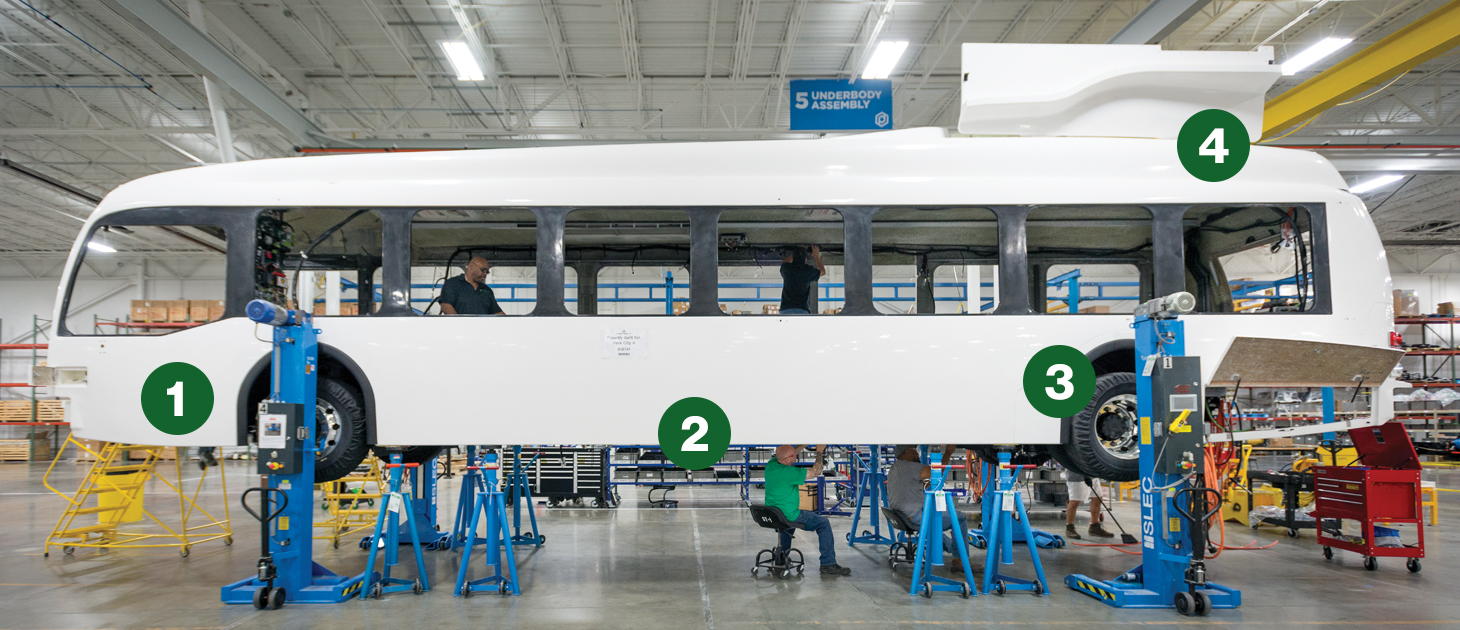
Proterra is the designer and manufacturer of zero-emission electric buses. Each Proterra model offers a range of energy-saving features including a battery pack and a charger.
1. BUS BODY
Available in 35- and 40-foot models, the body is made of a carbon-fiberreinforced composite. The Federal Transit Administration requires that heavy-duty large buses have a minimum service life of 12 years or 500,000 miles, but Proterra wants to extend that life expectancy. To demonstrate the durability of the body and other components, Proterra brought a vehicle to a testing facility that specializes in vibration, shock and multiple axis simulations. After a 750,000-mile simulation—the equivalent of 18 road years—the bus had “outstanding structural integrity,” says Matt Horton, Proterra’s chief commercial officer. “We think our bus bodies can last 50 percent longer than other bus bodies on the market.”
2. BATTERY PACK
This is the single most expensive component of an electric bus. “Depending on who you speak to in industry, the battery is about 15 percent of the cost of the vehicle,” says Horton. Proterra’s battery pack is about the size of two twin mattress. Led by Dustin Grace, a former battery engineer at Tesla, Proterra’s team is a multidisciplinary group of a couple dozen engineers with mechanical, electrical and chemical specialties. The battery pack helped Proterra achieve a record-setting distance last September, when the E2 travelled 603 miles on a single charge. The drive took place on a test track, without additional passengers; the upper end of the E2’s real-world range is 350 miles.
3. DRIVETRAIN
Forget about oil changes. Weighing less than one-tenth of a traditional diesel drivetrain, this component only has two moving parts: a permanent magnet drive motor and 2-speed auto-shift EV transmission. Proterra vehicles also have regenerative braking—lift your foot off the accelerator and the motor starts running backward, recapturing about 90 percent of the vehicle’s kinetic energy. “You’re basically running the motor as a generator,” says CEO Ryan Popple. “That feeling is a little bit different than coasting to a stop in a diesel bus.” As a result, Proterra has focused on additional training for drivers to help them understand why they shouldn’t jam on the brakes. “We don’t want them using the mechanical brakes very often, because it wastes energy, and brake pads and discs are expensive in this market,” Popple says.
4. CHARGER
The side of the bus includes a J1772 charging port (an industry standard used by Volkswagen, BMW and Ford, among others). But the bus’s roof holds the real magic. Proterra’s overhead charger does the job quickly—for the short-range bus (which can travel between 49–62 miles), a recharge can be completed in less than 10 minutes. In June 2016, Proterra opened up the patent on the overhead charger. “It gave our customers a lot of comfort that we’re very serious about creating an electric vehicle industry, as opposed to an electric vehicle monopoly,” Popple says. “We did it to show that we were confident we could compete without locking them into a certain charging protocol.” That’s reminiscent of an earlier decision by electric car maker Tesla. In 2014, Tesla announced an “open-source philosophy” toward all of its patents.
Read the full feature on Proterra in Middle Market Growth Summer 2017.